After three months of rigorous testing, Topsoe is ready to unveil the first batch of results from their SOEC test center. The demo, involving 12 stacks and 1200 cells, has successfully operated at a combined stack power of 350 kW. This power was maintained with high stability and efficiency over 2250 hours of operation. These findings are pivotal, highlighting the potential of SOEC technology to achieve exceptional efficiency and reliability at an industrial scale.
Innovative Strides in Frederikssund
In an exciting development for the future of decarbonization, Topsoe has announced significant progress from its Solid Oxide Electrolysis Cell (SOEC) demonstration facility in Frederikssund.
In the autumn of 2023, Topsoe's team started running the SOEC core’s first demonstration test under industrial conditions. Initiating this phase of testing marks a significant milestone for Topsoe, a company that first began exploring the potentials of solid-oxide electrolysis cells under Haldor Topsoe’s leadership in 1989. This is just the beginning.
Embracing transparency for collective progress
In creating technologies that will contribute to and shape the future of the energy transition, Topsoe acknowledges it as a shared responsibility to enable transparency and share learnings whenever possible. To those within the industry, Topsoe hopes this inspires, pushes, and heightens the shared results all strive to meet. To those outside of it, the company believes there is a right to understand the intricate technologies, systems, and processes that will soon be in the background of everyday lives.
To dive further into the world of SOEC and learn about the advancement of our manufacturing facility in Herning, Denmark, click here.
Impressive stability and efficiency demonstrated
After three months of consistent testing and monitoring, Topsoe is ready to share the first updates from its SOEC test center in Frederikssund. After 2250 hours of operation, with one core including 12 stacks running at approximately 350 kW total stack power, all 1200 cells have been shown to operate at high levels of stability, under industrial conditions, while maintaining stable temperature levels. While the full industrial use of SOEC technology will necessitate the testing of multiple cores, the results observed from this demo-size plant indicate a level of efficiency that is incredibly promising. Once scaled to meet industrial demand, this positions Topsoe's SOEC technology favorably for its high on-time performance and efficiency.
The consistent performance demonstrated in these test results signifies a significant achievement, highlighting the collaborative efforts of several key teams involved in the SOEC demonstration, as well as the broader contributions of the entire Power-to-X organization at Topsoe. These results mark an important milestone for the technology development team and represent a pivotal step forward in the validation of SOEC technology overall.
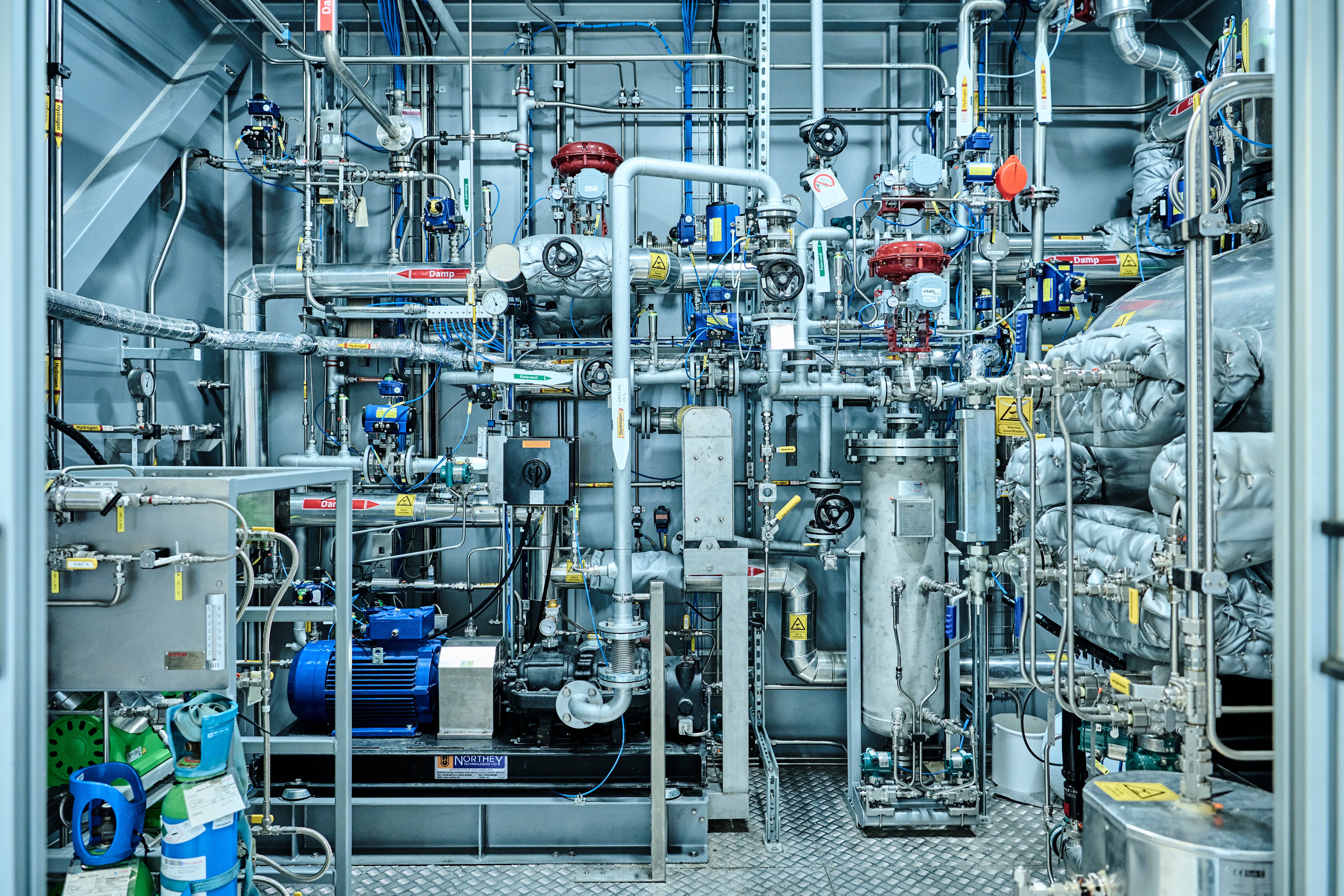
A look inside an industrial demonstration plant
The ultimate purpose of the SOEC demo test is structured to fulfill three key objectives:
1. Demonstrate complete hydrogen plant
First, the test serves as a demonstration for a complete hydrogen plant, showcasing how Topsoe’s SOEC core functions as an integral part in the broader scope of hydrogen production.
2. Validate performance of SOEC core
Second, this test serves to validate the performance of Topsoe’s SOEC core – closely monitoring variables such as cell voltage, current, pressure and temperature to understand the core’s overall performance, efficiency, and output.
3. Test industrially relevant design system
Finally, the test is conducted with an industrially relevant design system, using components and material selections pertinent to how this technology will be utilized in a fully industrialized setting.
The industrial purpose of this test was a critical starting point for the team in Frederikssund, as this was not merely a stack test but a comprehensive evaluation of a complete SOEC unit designed to operate under industrial conditions. This aspect is crucial because, unlike a regular stack test where variables can be tightly controlled to ensure optimal conditions for the components being tested, a test conducted under industrial conditions does not afford this level of control. Here, the team assesses how each component of the system performs in a setting that closely mirrors the operational realities this technology will face in actual production environments.
The industrial context of the test also extends to the individual components that comprise the SOEC core. Each component of the electrolyzer system, including the boiler feed water (BFW) system and the core’s steam generator, is tested under conditions that are industrially relevant.
Initial findings at 2250 hours of operation
The below graphs chart the SOEC core across cell voltage, current, pressure and temperature throughout its first 2250 hours of operation. The below results ultimately result in a consistent electrolyzer efficiency of around 93% (compared with LHV of Hydrogen) with an electricity consumption of the core at less than 36 kWh/kg H2 and a ramp up time from 0 – 100% load in 3 minutes.
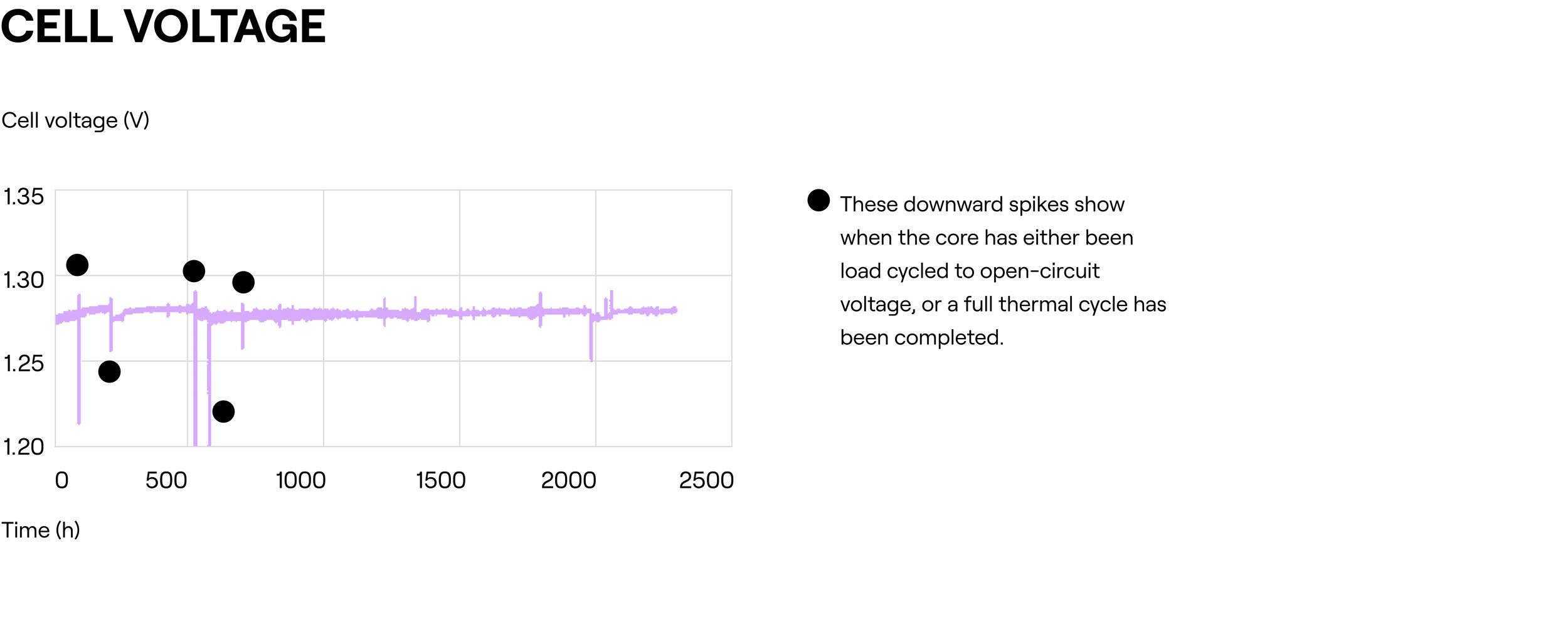
The above data shows the average cell voltage for all the 1200 cells in the 12 stacks as a function of time at operation. Throughout operation, the team aims at operating close to the thermoneutral voltage (VTN) to maximize efficiency. At this operating temperature, the VTN is slightly below 1.3V.
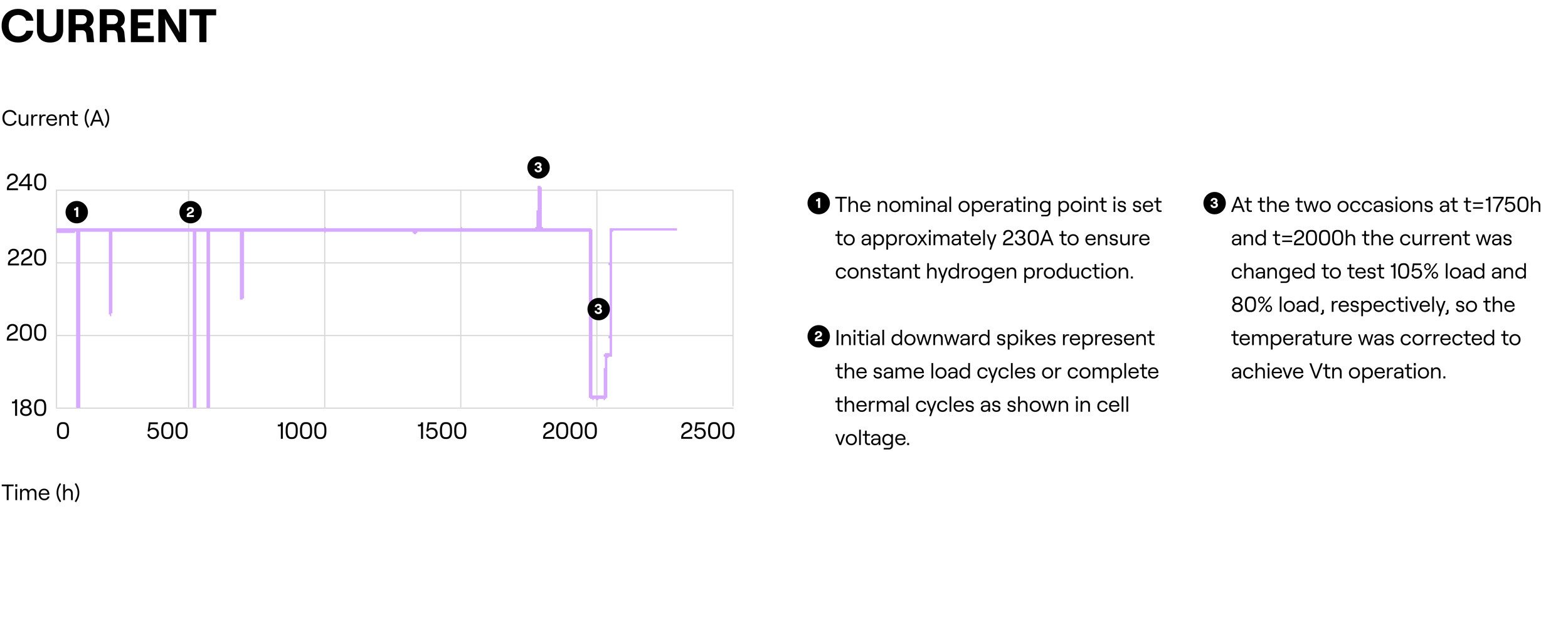
To operate with constant production of hydrogen, which according to Faraday’s Law is directly proportional to the current, the nominal operating point is set to approximately 230 A throughout each stack in the core.
The initial spikes downwards below 750 hours occur for the same reasons as explained in the figure above. At around 2000h the current was changed to 80% load where the temperature was corrected correspondingly to achieve thermoneutral operation.
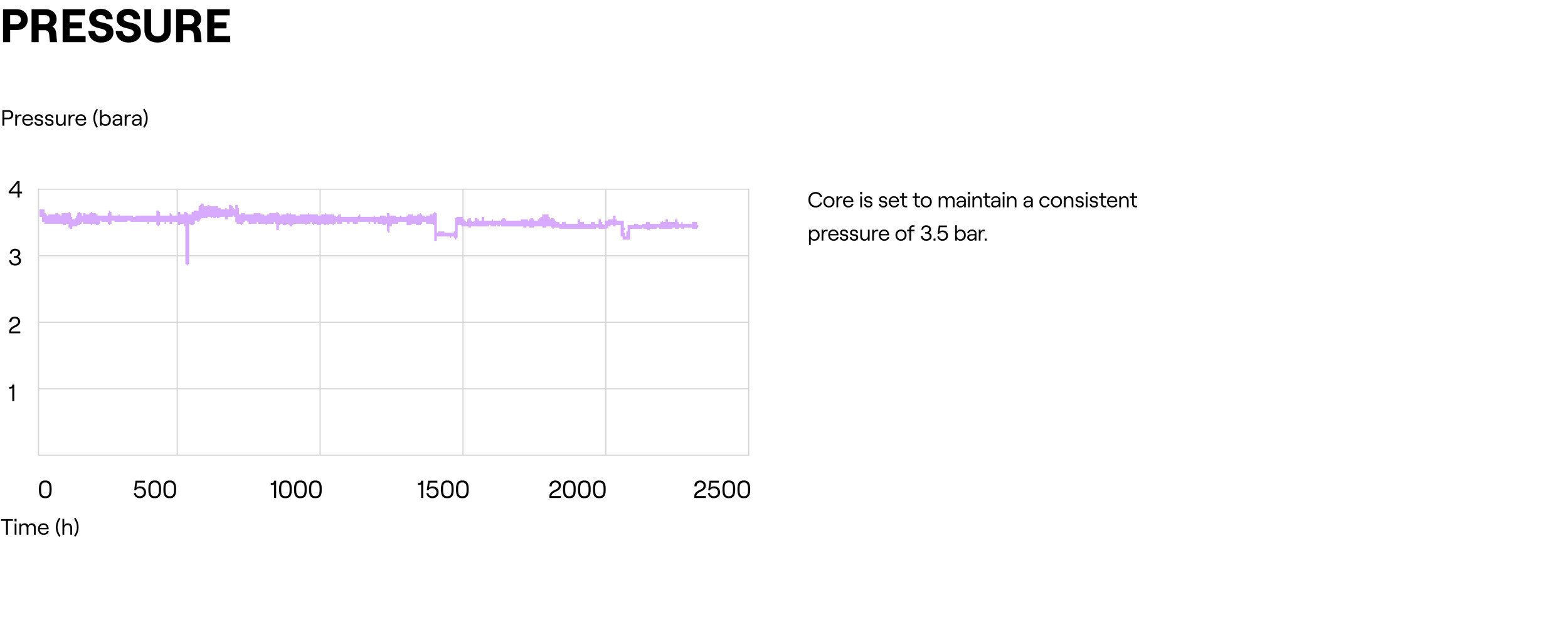
Throughout the demo test, the core is set to maintain operation at 3.5 bar. The data shows the pressure on the product side in the core at operation.
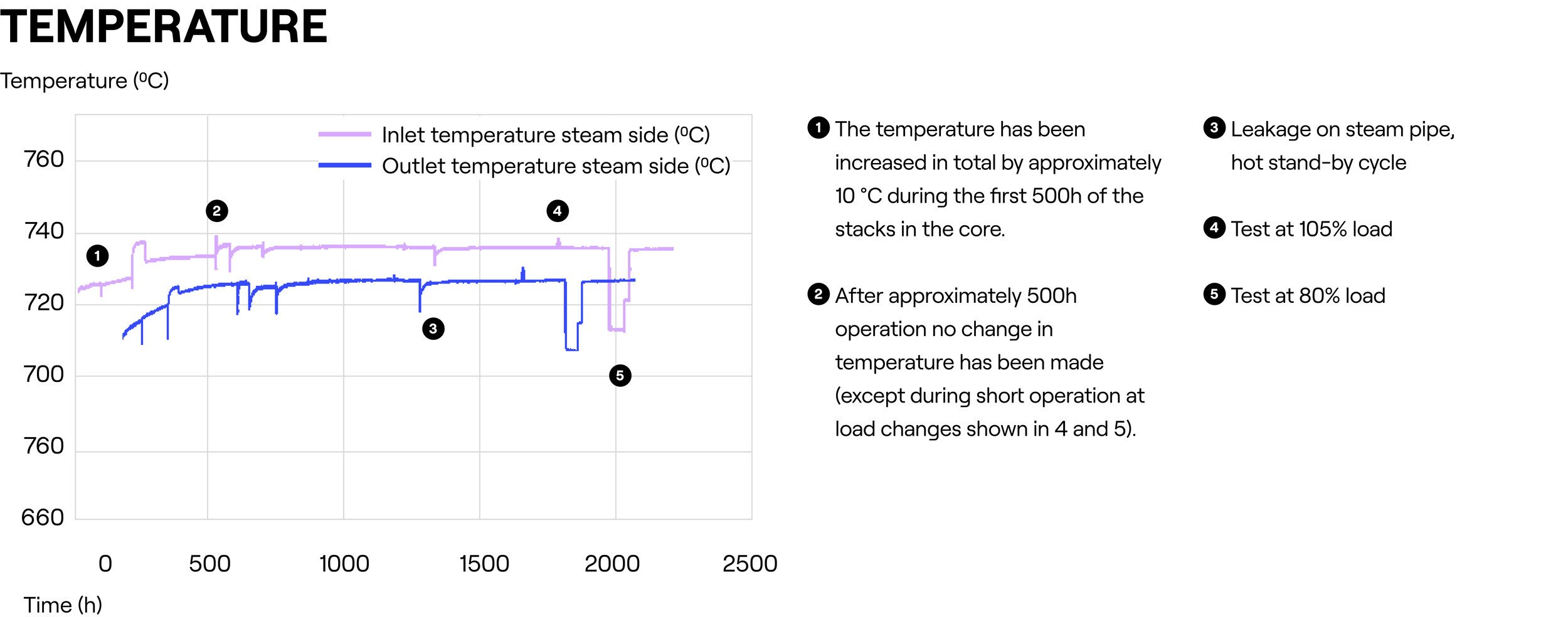
The test is aimed at operating in potentio-galvanostatic mode, meaning that voltage and current is kept constant by compensating load and degradation changes by changing the temperature of the inlet steam. A consistent temperature at constant current and voltage means a very stable performance of the stacks in the core with no degradation.
The data shows the inlet and outlet temperatures on the product side (steam/hydrogen) in the core at operation. The temperature increased in total by approximately 10 °C during the initiation phase of the stacks in the core. After approximately 500h of operation no change in temperature has been made (except during short operation at 105% load and 80% load).
Core takeaways: Robust performance and high efficiency
A key takeaway from the demo test in Frederikssund is the high levels of stability shown across the board of cell voltage, current, pressure and temperature. The tests have shown impressive stability at the current nominal operating point and have shown very little degradation at stack level throughout the duration of the test.
The tests have shown a high on-time factor with very few interruptions. The demo test in Frederikssund has demonstrated that with over 2250 hours of operation, Topsoe’s SOEC only had 150 hours of downtime, most of which was planned and none of which was due to the SOEC unit.
The test has also demonstrated high efficiency of around 93% at core level, making Topsoe’s SOEC solution 25%-30% more efficient than alkaline and PEM electrolysis alternatives. This efficiency is bolstered by a system that has shown itself to be robust to transients such as several start-ups, shutdowns and load changes. This efficiency is also based on an optimized electricity consumption of less than 36 kWh/kg H2 at the core, with a hydrogen LHV of 33.3 kWh/kg H2.
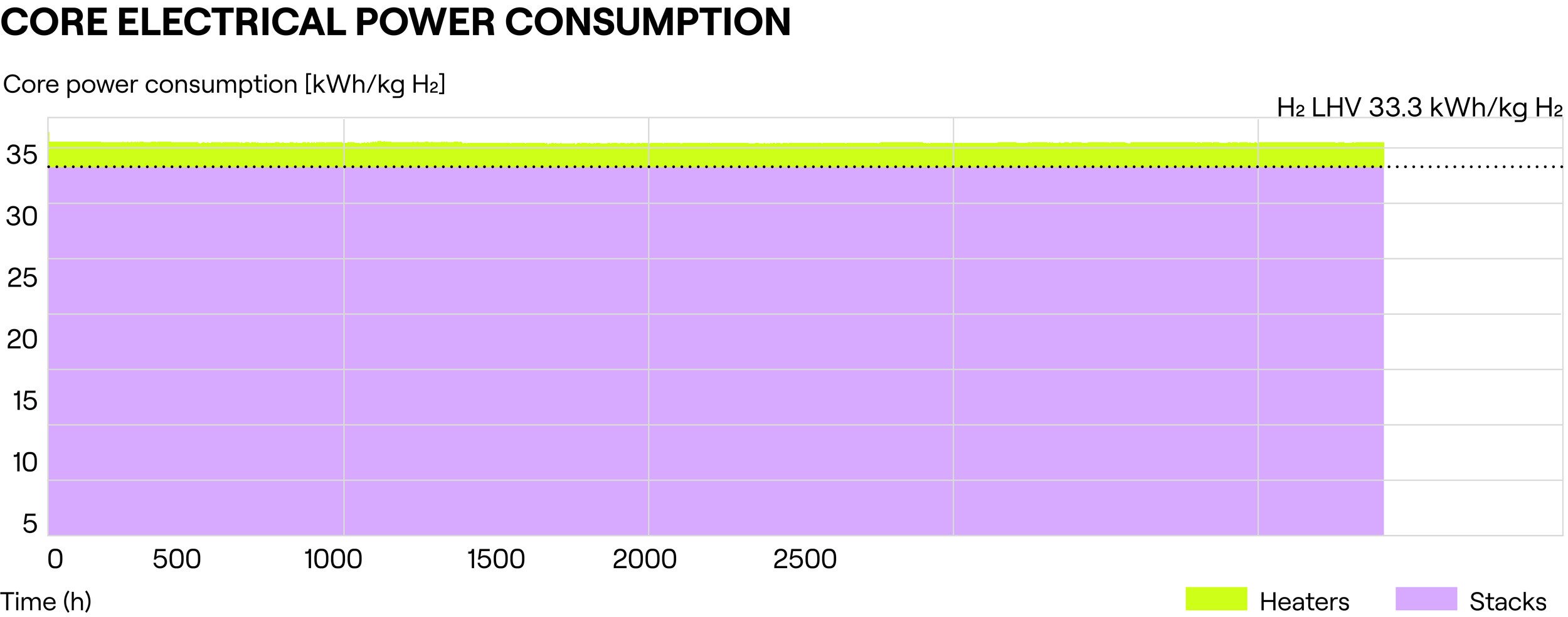
This stability, efficient electrical consumption, and resilience to a variety of changes is all essential for paving a marketable and impactful future for SOEC technology. With hydrogen’s production costs so closely tied to the price of its electrical feedstock, an electrolyzer’s efficiency is a make-or-break determinant for success. These early test results from Frederikssund illustrate that Topsoe’s SOEC electrolyzer is on its way to being a key technology in creating low-carbon and low-cost hydrogen.
A milestone towards green hydrogen
This demo test forms yet another important milestone in the development of SOEC electrolysis technology and in Topsoe’s wider mission to enable the energy transition by bringing efficient, scalable, and innovative decarbonization solutions to the market. The first phase of test results is representative of the tireless efforts of the team members at the Frederikssund testing facility. Topsoe is deeply proud of their hard work and commitment to continuously pushing and perfecting this technology.
Topsoe recognizes that the road to net-zero by 2050 will not be paved by any one single idea or technology. Like most complex problems that need to be addressed at a global scale, the energy transition can only be enabled through an ecosystem of complementary solutions that prioritize equitable, sustainable, and scalable energy systems. Topsoe is committed to making SOEC one of these solutions. With the remarkable results demonstrated by the demo team at Frederikssund, it is evident that after decades of development, SOEC technology is on its way to becoming a transformative technology in the energy landscape.