Prevent critical condenser corrosion problems
How to avoid inlet nozzle corrosion
Effect: Corrosion around the inlet nozzle
Cause: Incorrect insulation during inlet flange nozzle installation. The bricklined nozzle must not be covered with insulation or cladding plates since the inside of the nozzle is lined with acid resistant bricklining. External insulation can as well destroy the acid resistant membrane on the inside steel casing
Preventive maintenance guide:
1 The wall thickness of the casing for the bricklined acid collector should be ultrasonically checked regularly to ensure that the acid resistant bricklining is not damaged
2 Draw a grid on the acid collector bottom to ensure that the complete acid collector is checked. The grid can also be of great value for comparison of a specific area over time and hereby discover any suspicious changes. Internal cracks etc. in the bricklining can normally not be detected by visual inspection from the outside
3 Infrared measurements of the WSA plant in general are recommended to detect any hot spots indicating ineffectual insulation
If the corrossion is not observed in due time, it will expand and put pressure on the bricks inside the condenser. This will eventually destroy the glass tubes
Prevent internal corrosion
Effect: Corrosion around the internal tightening clamps and internal cover plates
Cause: The cooling air / shell side has been exposed to process gas
Preventive maintenance guide:
1 Inspect the area around the tightening clamps and replace insulation, if required, to secure a proper insulation in the critical area
2 The cooling air pressure at the outlet of the WSA condenser must always be higher than the process gas inlet pressure to the WSA condenser to prevent leakage of SO3 containing process gas from the tube side to the shell side of the condenser
3 The pressure difference must be 5 mbar and is controlled with help from a control damper positioned in the excess hot air duct to the stack. The necessary pressure is generated by the Cooling Air Blower, which is speed control operated.
4 The internals should be checked visually minimum once a year
How to spot corrosion
Corrosion on unprotected (internal) steel surfaces can be spotted as white/yellow deposits, iron sulfate, on carbon steel surfaces, or as green deposits, nickel sulfate, on stainless steel surfaces. The volume of the corrosion deposits are approximately 20 times the volume of the corroded metal, i.e. the extent of corrosion can initially be evaluated on basis of the thickness/volume of the deposits
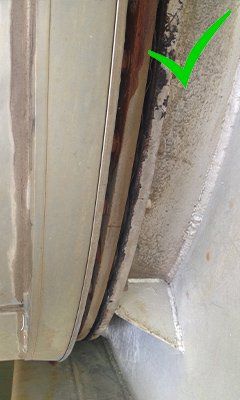 |
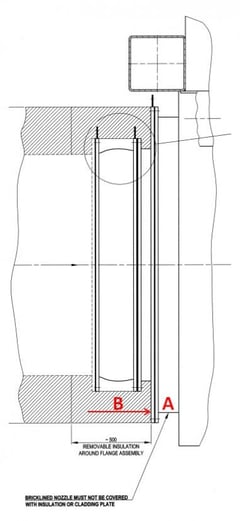
|
Picture1: Correct insulated - insulation to be stopped at flange connection |
Illustration 1: Correct way to insulate
A: No insulation or cladding,
B: Insulation to be stopped at flange connection
|
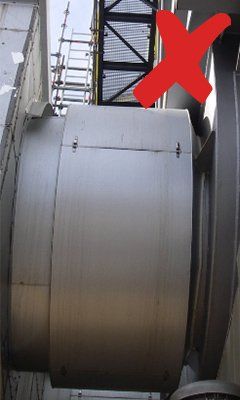 |
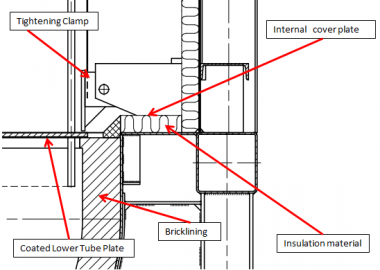 |
Picture 2: Incorrect insulated - process gas inlet nozzle is fully covered with insulation which may result in corrosion |
Illustration 2: Insulation placed inside the condenser |